Flax has its own nomenclature for all the stages from turning straw into a yarn or thread ready for spinning or knitting. The following methods describe both the use of simple hand tools from our starter kits and the use of the larger trestle mounted combined flax break, scutching and hackling unit based on cottage industry tools and suitable for those growing larger areas.
A good uniform crop will range in height from 800mm to 1200mm high.
Commercial yields of dry straw in Europe range from 5–10 tons to the hectare.
Based on an average of 7.5 tons of dry straw the amount of fibre per area you can expect:
Area 1 hectare 100 sqr. mtrs. 1 metre
Long fibre spinning 14% 1050 kg 10.5 kg 100 grams
Tow short spinning 14% 1050 kg 10.5 kg 100 grams
Seed 12% 900 kg 9 kg 90 grams
Shive 40% 3000 kg 30 kg 30 grams
Chaff 20% 1500 kg 15 kg 15 grams
Time to break scutch and hackle (unpowered tools per person) 3 years 100 hours 2 hours
In the days of hand working, an acre of flax would employ two people fully for a year. It will take around a day to break, scutch and hackle 1 kilo of long line fibre and 1 kilo of tow from retted flax stems, using hand tools.
Breaking this is the first process which breaks the outer stem and removes the bark which falls off in lengths of about 30 mm this material is called shive. On a small scale this can be achieved in part without any tools by just holding the fibre and a mechanical action between your two hands. On a bench a block placed across some fibres which are the bent up to break the straw, the block is moved along 5 mm at a time to create a crimping action.
The traditional cottage industry break (pictured right) applies more force and works like a blunt guillotine and applies a number of crimps in one go. The next machine for the larger producer is the roller break which is most efficient.
Scutching is a scraping action which removes most of the remaining shives and loosens dust and dried gums which are stuck to fibres. When working flax, it is important to keep the root ends together. Hold one end of the bunch of stalks; the aim is to hold one third and work two thirds, grip the stalks firmly and wrap around the around your hand. With the hand block start scraping the fibres from the centre right to the end away from you. Use the sharpest edge on the block, when all the shive is removed turn the stalks around and scutch the other end.
On the larger break the scutched flax is held vertically and beaten briskly with a scutching stick.
Hackling is passing the fibres through a series of combs from coarse to fine; this process removes the shorter fibres, straightens and further cleans fibres. At least half of the fibres after scutching will be removed. These shorter fibres are referred to as tow and can be further carded and spun in the same way as wool. Once again hold firmly working each end individually holding one third.
Start with the coarse combs working down to the finest. When using the hackling combs fixed vertically the fibres are dropped over these in stages for hackling. Lengths of long line flax fibres prepared for spinning are called stricks. After hackling expect between 33 to 50 % of the fibre will be long the rest will be tow.
Distaff preparation
Before long flax fibres can be spun they need to be held in such a way that they feed out continuously to the drop spindle or spinning wheel. These are held on a distaff the most common shape of these is the cone distaff which can readily be made from card. A strick of fibre is tied with a long ribbon and then swept backwards and forwards on a table creating a fan shape. The fibres are picked up by the cone as it is rolled over them, the ribbon is laced around the fibres.
The fibre is now ready for spinning with a drop spindle.
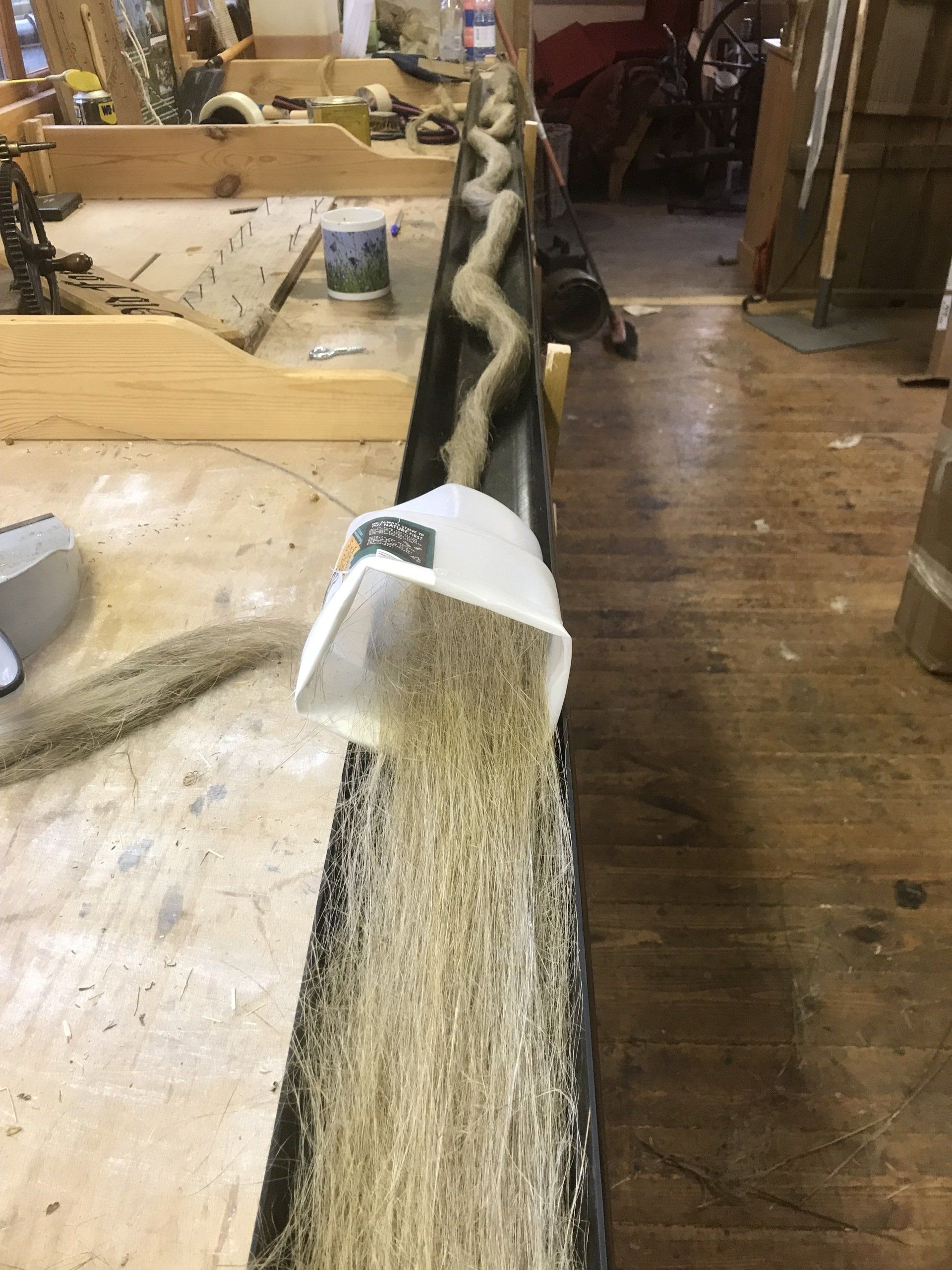
Making Sliver sliver is a continuous ribbon of fibres often used in industrial spinning. We have found that using sliver when spinning with a wheel or drop spindle has improved the quality and speed of our own spinning and the teaching of others to spin. We now use commercially available sliver (see store) for practice and teaching spinning. We make our own sliver using home grown stricks of flax which are drawn out in layers along a channel. In addition to improving the efficiency of spinning it gives the option of blending fibres when working on joint projects, or if you are using flax stricks which are not consistent. To present the sliver for spinning we have designed a new type of distaff flaxland sliver distaff to hold the fibres in tension and position which greatly aids the process.
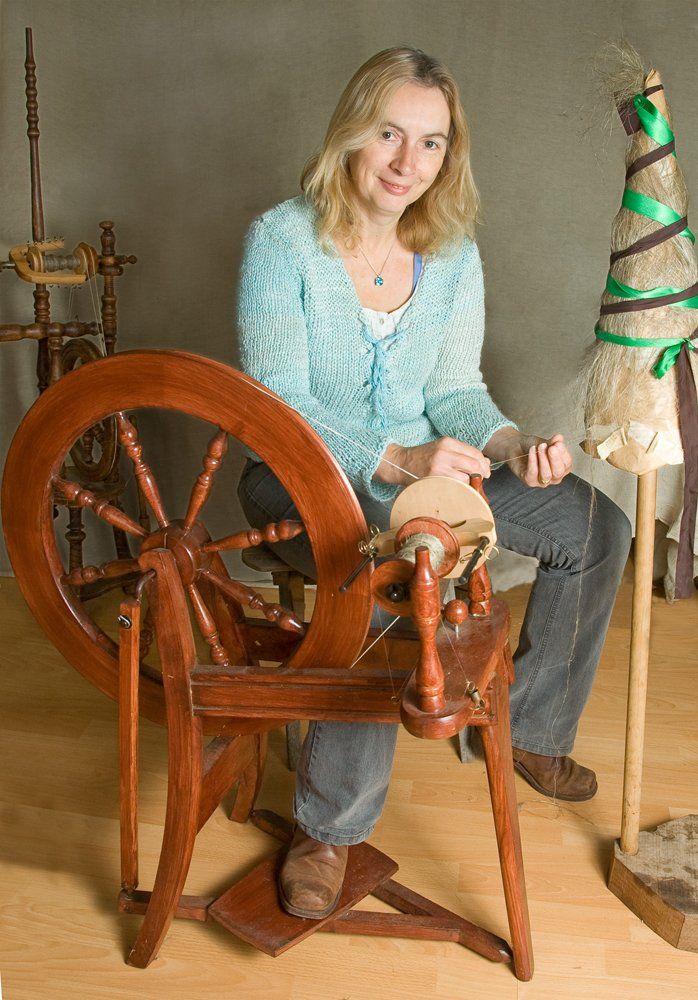
Spinning longline flax
well grown and prepared flax is a delight to spin either with a drop spindle or a wheel. With experience flax has the ability to continuously draw from the mass of fibres. The twisting action from the wheel catches fibres which can be spun either finely or coarsely as required.